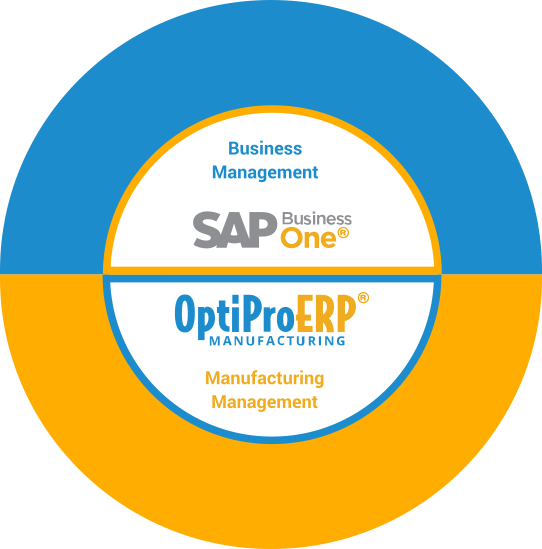
(Before getting into Inventory Management, it’s important to understand what the word ‘inventory’ means). There are three types of inventory to include: Raw Materials, Work in Process, and Finished Goods. Raw Materials are stock used to make an end product. Work in Process consists of the raw materials that are being made into finished goods. And, Finished Goods are the final products that get produced for sale to consumers.
Inventory management tracks how much physical inventory you have in your organization. It monitors stock at other locations, such as distributors or subcontractors. When you have clear visibility into your inventory, you know when to order, where to store it, and when you need to stop selling.
Managing inventory is an important part of business administration. If you have excess inventory, money is being wasted (which is referred to as underutilization.) If you don’t have enough, it delays deliveries. Neither one is a good scenario.
An inventory management system tracks inventory availability at all points of your supply chain — from purchasing, to production, and finally sales to consumers. An inventory management system is important for companies with large amounts of inventory in order to keep it at optimal levels.
Products get scanned using bar code or RFID (radio frequency identification) systems. This information gets sent to the Inventory Management System to keep track of how much product is being sold and what is in the warehouse.
The system supports electronic data interchange (EDI). EDI sends and receives data between two parties using data transmission lines, i.e. the Internet. It allows communication with vendors to buy materials.
Products get scanned using bar code or RFID (radio frequency identification) systems. This information gets sent to the Inventory Management System to keep track of how much product is being sold and what is in the warehouse.
The system supports electronic data interchange (EDI). EDI sends and receives data between two parties using data transmission lines, i.e. the Internet. It allows communication with vendors to buy materials.
Traditional inventory management becomes problematic as a company grows. It includes supplier agreements to get discounts for consistent orders over specific periods. This often results in ordering more than needed to fulfill production needs. It can also lead to vendor lock-in, obligating you to long-term relationships with suppliers.
Traditional inventory management entails manually checking stock levels to know what is running low. This is time-consuming, prone to errors, and not efficient. To reorder inventory, your purchasing department has to call, email, fax, or use an online system. Again, this uses more employee time than an automated inventory system would.
Warehouses become necessary to store excess inventory. Items that are perishable, hazardous, or require refrigeration need special accommodations. These concerns create additional expense, along with warehouse personnel and theft protection.
Pre-delivered information views represent different aspects of your business performance. Use tailored reporting capabilities to analyze the data most relevant to your KPIs.
Inventory is a big expense that must be carefully managed. It directly affects your customers — so knowing how much you have on hand at all times is essential. Since inventory levels change constantly, tracking them manually isn’t practical. Modern inventory management systems incorporate new technology to efficiently monitor inventory and manage the supply chain.
When you have optimal inventory levels, you won’t lose out on missed sales. A modern inventory management system tracks inventory in real time. It allows you to see what is selling well and place orders for more inventory before you run out. You can also set minimum levels to notify you when inventory is getting low and it is time to order.
With a modern inventory management system, you no longer rely on manual counts. It helps you keep up with change as your business grows. It keeps track of your stock in all locations and seamlessly integrates with other systems to scale operations.
It’s easy for people to miscalculate with manual inventory counts. That can result in too much or too little stock. When processes are automated, there’s less chance for human error. With an inventory management system, scanners can count inventory. The information gets stored for decision-makers to view. It reduces errors and increases efficiency, making inventory tracking faster and more accurate.
Having optimal inventory on hand allows you to fulfill orders on time. No more missing deliveries due to out-of-stock items. Thus, efficient inventory management improves customer satisfaction and retention. You can also add to your customer base with a better brand reputation.
With a modern system it's easy to locate items. You can organize your products based on demand for a more streamlined warehouse. With less time looking for things, your workers have more time to spend on activities of greater value for the company. Modern inventory management gives your purchasing department real-time synchronization of inventory receipts and levels. Replenishment orders get placed when needed.
Access to real-time inventory levels allows you to spot problems. At a glance you can see your safety stock, re-order points, cycle counts, and demand planning. You can also determine what’s on order and the due date of every production order. It provides analytics, revealing the most profitable products and the best sellers. You can also determine the location or time of year that has the best results.
Having too much inventory obliges you to shoulder the cost for items that are not used. Having too little inventory causes you to delay or even cancel customer orders. Either scenario costs your business money. Having the optimal amount of stock means you don’t have the expense of storing items. What is more, you don’t incur labor for manually counting or searching for products.
A modern inventory management system uses AI and machine learning technologies. It makes predictive analysis and demand forecasting more accurate. With this knowledge, you can get better pricing, since you’ll know how much and how often to order.
To achieve the greatest results, it’s important to use best practices as described below.
ABC Analysis is a method that keeps stock in a hierarchy to make it manageable. “A” items would be the top sellers. “B” would be the next level of priority. The “C” level would be those items that are low-priority and not ordered as often. This method will help keep your inventory organized and streamlined.
Pick and pack involves laying out your warehouse for efficiency. Have the most used items closest to where they get packed. Keep the warehouse clean and organized. Double-check each order, and use barcodes or RFIDs on inventory to keep track of levels. If you use a warehouse management system (WMS), pickers are shown exactly where to find items.
Key Performance Indicators (KPIs) allow you to track activity and help you make decisions. Inventory carrying cost, write-off and write-down, rate of turnover, cycle time, order status, tracking, and fill rate are KPIs to watch.
A reorder point formula defines when to order more inventory. This formula is: (average daily unit sales x average lead time in days) + safety stock = reorder point. Using this formula will help you to keep only the necessary inventory in stock
It’s good to keep a small amount of excess inventory. It helps to avoid running out if you have an influx of orders or a change in supplier lead time. Safety stock ensures you don’t lose customers or revenue from being unable to fulfill orders.
It’s important to understand how demand affects product turnover. By using a formula, you can know what inventory is not moving and figure out how to get it sold. To calculate inventory turnover, use this formula: Cost of Goods Sold ÷ Average Inventory.
It’s important to optimize the inventory counting process. Schedule inventory counts when it is less likely to interrupt business operations. Make sure everything in the area is clean and organized. Also, know exactly what should get counted to ensure nothing gets missed.
It’s important to keep tight control over your inventory. Low inventory reduces holding costs, allows for more space, reduces the risk of product obsolescence, and makes it easy to find items. Keep an eye on which products sell the most and make them easy to access. Review historical records of your safety stock levels to see if you need to make adjustments.
It’s important to have good working relationships with vendors. They are more likely to accommodate you if you run into a problem and need something quickly. Make sure your vendors are paid promptly and maintain good communications with them.
An inventory management system is very important to your business. It removes error-prone manual processes and incorporates best practices. It helps improve operations throughout an organization.
Inventory management systems have many features, but the most common are below.
Inventory control keeps track of items on the warehouse floor. It categorizes by type, location, and SKU. This helps to audit data, to generate reports, and to search, filter, and view products.
Handles administrative functions and integrates with other software if needed.
Inventory tracking keeps tabs on orders in transit, giving you end-to-end visibility into your supply chain. It integrates with your suppliers’ systems to automatically reorder items when supplies are low. It allows customers to receive information on what products are available and when.
To make it quick and easy to track, the software integrates with barcode scanners to identify and label products.
This part of the system allows you to take control of your inventory needs. It provides automated reports that show trends and changes to the supply chain. It keeps exactly the right amount of inventory on hand.
Receive alerts when inventory falls below or rises above predefined levels. If there is a delay anywhere along the supply chain there is also a trigger. Having these notifications lets you reduce waste, manage costs, and keep customers informed.
To get the most from an inventory management system, consider the following features. They will allow your business to compete in today’s fast-changing marketplace.
The best way to know what your business needs from an inventory management system is to identify your problem areas. Once you have this information, it is easier to know what functionality you’ll need as you look for systems.
There are lots of inventory management systems on the market. Will you need to connect to other existing systems? If so, you’ll want to ask vendors if their system can integrate. You’ll also want to learn what’s involved with the transition, how the vendor will assist you in the change from manual to automated processes, and what level of training is offered.
You’ll want to understand all of the costs involved in implementing the new software. Make sure it can handle what you currently process while having plenty of room for growth. If you are connecting systems, your in-house IT will need to manage updates to ensure the systems continue to work together. Be sure your IT staff has the capability.
Determine any hardware costs, user fees, and upgrade or maintenance costs. Find out how much training they provide.
If you are looking to integrate many systems, it may make sense to consider an Enterprise Resource Planning (ERP) solution. An ERP system integrates all aspects of your operation – from planning to production to purchasing. Instead of connecting several different systems, you use one system and database. That way, you can manage your entire operation and optimize your inventory.
The most common ERP modules are Human Resources, Inventory, Sales/Marketing, CRM, Purchasing, and Finance/Accounting. ERP helps companies unify critical business functions and optimize operations. Its organization-wide visibility helps detect inefficient processes and reveals growth opportunities.
Review the gains you will receive from a warehouse management system to help you determine your budget. You should receive a return on your investment in the form of:
Look for systems that will perform the functions most important to your organization. Some of the essentials you’ll want are:
OptiProERP is a complete manufacturing ERP solution embedded into SAP Business One. It provides business and manufacturing functionality, including robust inventory management features. OptiProERP is mobile-friendly and cloud-based. It provides demand forecasting, IoT integration, machine learning, and AI. OptiProERP also includes e-commerce and warehouse management modules.
Manufacturers need full integration between their accounting department and their purchasing and manufacturing operations in order to run a truly efficient organization. OptiProERP, an ERP system specific to the manufacturing industry, has strong accounting and financials as well as shop floor execution, inventory management, and job costing. Get immediate access to both financial and shop floor data to help you have shorter production runs, keep up with product changes, and deliver a personalized customer experience.
OptiProERP is built on SAP Business One, the market-leading platform for small and midsize enterprises. It extends the platform to provide a more advanced, fully integrated, end-to-end solution designed specifically for manufacturers.
After 15 years of steady growth, DACSA (Design, Automation and Centrifuges), a manufacturing business that modernizes sugar centrifuges in the sugar mills of Mexico, had outgrown the manual processes they used to run the business.
DACSA needed advanced manufacturing functionality to help them fully cost the products they were delivering, including sub-contracted services. They also needed the ability to manage parallel processing in order to meet delivery deadlines.
DACSA relies on OptiProERP to standardize processes, define distribution channels and automate manufacturing processes. Focused on continued growth, DACSA relies on the continuous quality system checks from OptiProERP to meet their aggressive goals.
eWorkplace Manufacturing, Inc. is a global provider of market-leading, industry-specific software and services focused on the manufacturing and distribution industries. Through its innovation and deep industry expertise, eWorkplace Manufacturing delivers industry-focused solutions that address the unique challenges of discrete and process manufacturers and distributors.
We want to hear from you!
(949) 340-7262